Understanding Injection Molded Plastic Products: Transforming Manufacturing Efficiency
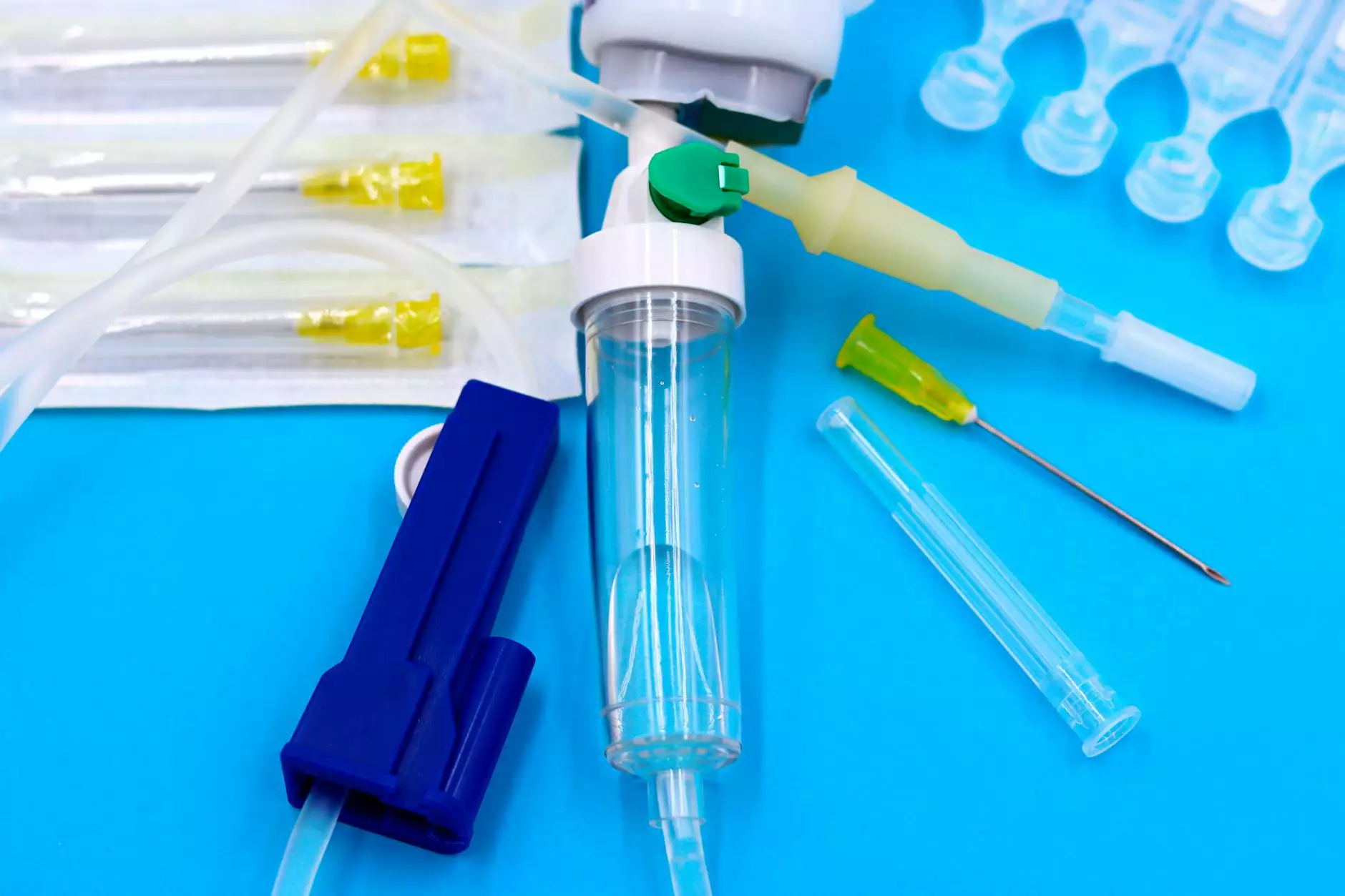
Injection molded plastic products are taking the manufacturing world by storm, providing an efficient, cost-effective solution for businesses in various industries. At Sumiparts, our expertise in machining, laser cutting, welding, plastic injection, vulcanized processes, and industrial supplies positions us as leaders in the production of high-quality plastic components that meet diverse application needs.
What Are Injection Molded Plastic Products?
Injection molding is a manufacturing process for producing parts by injecting molten material into a mold. The injection molded plastic products produced through this technique are renowned for their durability, precision, and versatility.
The Injection Molding Process
The injection molding process can be divided into several key steps:
- Material Preparation: The raw plastic material, often in the form of pellets, is fed into a heated barrel where it is melted.
- Injection: The molten plastic is injected into a mold under high pressure, ensuring that it fills all cavities.
- Cooling: Once the mold is filled, the plastic is cooled to solidify it.
- Mold Release: After cooling, the mold is opened to release the finished product.
Materials Used in Injection Molding
A variety of plastics can be used in injection molding, including:
- Thermoplastics: Such as polyethylene, polystyrene, and ABS, which can be re-melted and reprocessed.
- Thermosetting Plastics: Such as epoxy and phenolic resins, which cannot be remelted once set.
Advantages of Injection Molded Plastic Products
The use of injection molded plastic products offers numerous advantages that contribute to their widespread adoption across industries:
1. Cost Efficiency
Injection molding allows for mass production of components at a lower cost per unit. The initial setup may be high, but the low costs of materials and high-speed production offset this expense over large production runs.
2. Design Flexibility
Plastic injection molding permits a high degree of design freedom, enabling manufacturers to create complex shapes and intricate geometries that other manufacturing methods may struggle to achieve. This flexibility allows for innovative product designs.
3. High Precision and Consistency
The precision of the injection molding process ensures that each product manufactured is nearly identical, which is crucial for applications requiring tight tolerances.
4. Rapid Production Speeds
Once the molds are created, production can occur at astonishing speeds, enhancing productivity and allowing for quick product turnaround times.
5. Reduced Waste
The efficiency of injection molding results in minimal material waste, which is both economically and environmentally beneficial.
Applications of Injection Molded Plastic Products
The application of injection molded plastic products spans a multitude of industries, showcasing their versatility:
1. Automotive Industry
Injection molded components are widely used in the automotive sector, from dashboards to bumpers, providing lightweight yet durable parts that can withstand demanding conditions.
2. Consumer Goods
Many everyday products, including containers, toys, and household items, rely on injection molding for efficient mass production.
3. Medical Devices
The precision and hygienic nature of injection molded parts make them fundamental in the production of medical equipment and devices.
4. Electronics
From casings to components, many electronic devices incorporate injection molded parts that ensure both aesthetic appeal and functional integrity.
Choosing the Right Injection Molding Partner
When considering the use of injection molded plastic products, selecting the right manufacturing partner is crucial to your success. Here are some factors to consider:
1. Expertise and Experience
Look for a supplier like Sumiparts with extensive experience in both design and production to ensure the finest quality of products.
2. Advanced Technology
Cutting-edge technology in machinery and software can greatly enhance the precision and efficiency of the injection molding process.
3. Customization Capabilities
Your manufacturing partner should be able to offer customized solutions tailored to your specific application needs.
4. Quality Assurance
Ensure the supplier has a rigorous quality assurance process to maintain high standards in production and mitigate risks.
Conclusion
In conclusion, the robust world of injection molded plastic products is designed for innovation and efficiency. Leveraging this manufacturing process can significantly enhance productivity while ensuring high-quality output across a range of industries. As manufacturers strive to meet ever-increasing demand for precision and efficiency, the role of injection molding continues to expand, making it a critical component in contemporary manufacturing.
Partner with experts like Sumiparts to unlock the full potential of injection molded plastics in your business ventures today!